Blog
How Shingles Are Manufactured: The Process Explained
Shingles play a critical role in protecting homes from weather, yet most homeowners rarely think about how they’re made. From the materials used to the manufacturing process, shingles have evolved significantly over time. Understanding the production of shingles can help you make more informed decisions when it’s time to replace your roof. Avenue Roofing, a trusted name in Jacksonville, FL, specializes in shingle roof installations and replacements, and we’re here to break down the step-by-step process of how modern shingles are made.
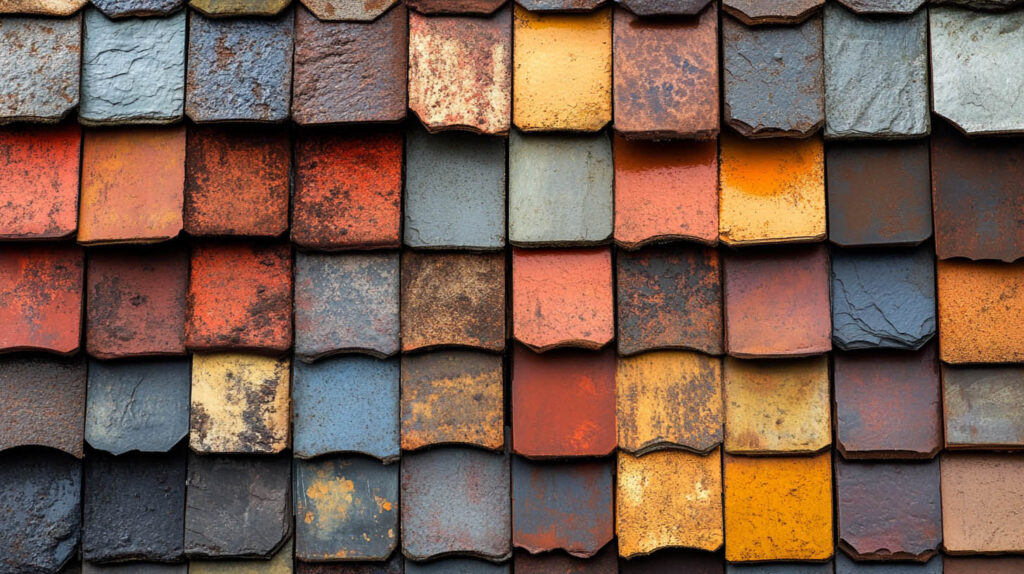
The History of Asphalt Shingles
Asphalt shingles, the most popular roofing material in the U.S., have been around since the early 20th century. These shingles were initially made by dipping paper in tar. Over time, improvements in technology have led to more durable and fire-resistant products.
Historically, tar has been used as a waterproofing agent for thousands of years. It was first utilized in canals and brick structures and later found its way into roofing materials. By the 1950s, asphalt shingles as we know them today became widespread. Early shingles were made from organic felt, but due to weight and fire concerns, manufacturers shifted to fiberglass-based shingles, which are now the standard.
Materials Used in Shingle Manufacturing
1. Fiberglass Mat
The foundation of modern asphalt shingles is a fiberglass mat. Fiberglass is preferred because of its lightweight, fire-resistant properties. The mat forms the base of the shingle, providing structure and durability. This material replaced asbestos, which was once used for fire resistance but was phased out due to its health hazards.
2. Asphalt Coating
Once the fiberglass mat is formed, it’s coated in asphalt, which is derived either from natural deposits or as a byproduct of crude oil refining. The asphalt coating makes the shingle waterproof and durable. To enhance stability and fire resistance, materials such as finely ground limestone or fly ash are added to the mix.
3. Mineral Granules
After the asphalt coating, the top surface of the shingle is embedded with ceramic-coated mineral granules. These granules come in a variety of colors and serve multiple purposes:
- UV Protection: Granules help protect the shingles from harmful ultraviolet rays, prolonging their lifespan.
- Fire Resistance: The addition of these granules increases the fire resistance of the shingles.
- Aesthetic Appeal: The granules give shingles their distinct color and texture, allowing homeowners to choose a roof that complements the design of their home.
For areas with high humidity, manufacturers may also add copper to the shingles. Copper helps prevent algae growth, which can cause unsightly black streaks on roofs.
4. Adhesive and Backing
To prevent shingles from sticking together during storage and transportation, the backside of each shingle is coated with a layer of sand or talc. Additionally, strips of thermoplastic adhesive are applied. Once the shingles are installed, the heat from the sun activates the adhesive, creating a stronger bond between shingles and enhancing wind resistance.
The Shingle Production Process
Step 1: Coating the Fiberglass Mat
The manufacturing process begins by saturating the fiberglass mat with asphalt. The mat is fed through large rollers that evenly coat the material, ensuring durability and waterproofing. This step is crucial for creating a solid foundation for the finished shingle.
Step 2: Adding Stabilizers
Once the mat is coated, stabilizers such as limestone or fly ash are added. These materials not only make the shingles more durable but also improve their fire resistance. By reinforcing the asphalt, stabilizers help extend the lifespan of the shingles.
Step 3: Embedding Mineral Granules
Next, ceramic-coated mineral granules are embedded into the top layer of the shingle. These granules provide UV protection, increase fire resistance, and add color to the shingle. The granules are pressed into the asphalt while it’s still hot, ensuring they adhere securely to the surface.
Step 4: Cutting and Shaping
After the granules are embedded, the shingles are cut to size. The cutting process also creates tabs, which interlock the shingles when installed on a roof. These tabs play an important role in preventing wind from lifting the shingles off the roof.
Step 5: Adhesive Application
Strips of thermoplastic adhesive are applied to the back of each shingle. These adhesive strips activate when exposed to heat, allowing the shingles to stick together more firmly once installed. This step is vital for preventing wind damage.
Step 6: Packaging and Byproduct Reuse
Once the shingles are cut and shaped, they’re packaged and prepared for distribution. Any byproducts, such as excess asphalt or cutouts from the shingles, are often recycled and sold to asphalt road paving companies. This eco-friendly approach helps reduce waste in the production process.
Benefits of Modern Shingles
Modern shingles offer several advantages for homeowners, including:
- Durability: Asphalt shingles are known for their ability to withstand various weather conditions, including heavy rains, snow, and high winds.
- Affordability: Asphalt shingles are one of the most cost-effective roofing options available.
- Low Maintenance: These shingles require little maintenance compared to other roofing materials like wood or metal.
- Versatility: Shingles come in a wide range of colors and styles, making it easy to find an option that complements your home’s exterior.
Unique Fact: According to the Asphalt Roofing Manufacturers Association (ARMA), approximately 80% of U.S. homes are roofed with asphalt shingles, making it the most popular roofing material in the country.
Why Choose Asphalt Shingles?
Asphalt shingles are a popular choice for homeowners due to their affordability, durability, and ease of installation. In areas like Jacksonville, FL, where extreme weather conditions can take a toll on roofs, asphalt shingles provide a long-lasting and cost-effective solution. Their fire-resistant and weatherproof properties make them a reliable choice for homes in hurricane-prone regions.
If you’re considering a roof replacement, Avenue Roofing specializes in installing high-quality asphalt shingles that can withstand Jacksonville’s unpredictable weather conditions.
FAQs
1. How long do asphalt shingles last?
Asphalt shingles typically last between 20 to 30 years, depending on the climate and installation quality.
2. Can asphalt shingles be recycled?
Yes, asphalt shingles can be recycled and often repurposed for road construction, reducing landfill waste.
3. Are asphalt shingles resistant to fire?
Yes, asphalt shingles with a fiberglass mat base are highly fire-resistant, making them a safe option for most homes.
4. What is the difference between asphalt and composite shingles?
The terms are often used interchangeably. Composite shingles usually refer to those made from a mixture of materials like asphalt, fiberglass, and granules.
5. How often should I inspect my asphalt shingle roof?
You should inspect your roof at least twice a year, especially after storms, to check for damaged or missing shingles.
Conclusion
Understanding how shingles are made provides valuable insight into why they are so effective at protecting your home. From the materials used to the detailed manufacturing process, modern shingles are designed for durability, fire resistance, and aesthetic appeal. If you’re in need of a new roof, consider asphalt shingles for their proven reliability and long-lasting protection.
To learn about the 7 most common causes of roof leaks, click here.